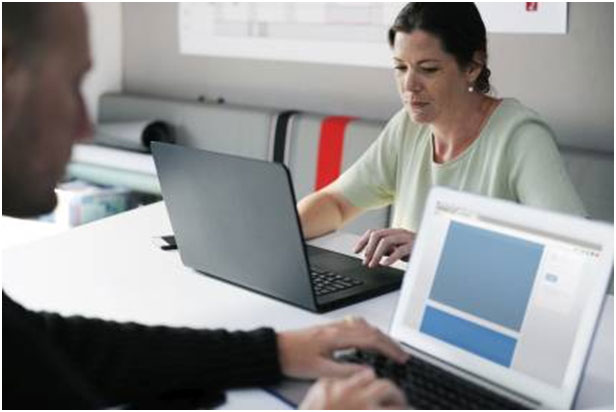
Information related to the accountability objectives tells what end results the job exists to achieve and the incumbent is held accountable for. There are four areas of accountability: organization (including staffing, developing, and maintaining the organization) and strategic planning, tactical planning, execution and directing the attainment of objectives, and review and control. Because the Hay Plan is based on information gathered in an interview (as opposed to the checklist method in the Management Position Description Questionnaire, MPDQ, for example) the success of the Hay Plan depends upon the skills of the interviewer. Interviewers can be trained, however. The Hay Plan continues to grow in popularity.
Functional Job Analysis (FJA) is another standardized approach. It was developed by the United States Training and Employment Service (USTES) to describe the nature of jobs and to develop job summaries, job descriptions, and employee specifications. FJA, originally meant to improve job placement and counseling for workers registering for employment at local employment offices, was part of an intensive research program directed toward producing the 1965 edition of the Dictionary of Occupational Titles (DOT). Today, many aspects of FJA are used by a number of private and public organizations.
FJA is both a conceptual system for defying the dimensions of worker activity and a method of measuring levels of worker activity. The basic premises of the FJA are:
- A fundamental distinction must be made between what gets done and what workers do to get things done. Bus drivers do not carry passengers; they drive vehicles and collect fares.
- Jobs are concerned with data, people, and things.
- In relation to things, workers draw on physical resources; in relation to data, on mental resources; and in relation to people, on interpersonal resources.
- All jobs require the worker to relate to data, people, and things to some degree.
- Although the behavior of workers or the tasks they perform can apparently be described in an infinite number of ways, there are only a few definitive functions involved. Thus, in interacting with machines, workers feed, tend, operate, and set up; in the case of vehicles or related machines, they drive or control them. Although these functions vary in difficulty and content, each draws on a relatively narrow and specific range of worker characteristics and qualifications for effective performance.
- The functions appropriate to dealing with data, people, or things are hierarchical and ordinal, proceeding from the simple to the complex. Thus to indicate that a particular function, say compiling (data), reflects the requirements of a job is to say that it also includes the requirements of lower functions, such as comparing, and that it excludes the requirements of higher functions, such as analyzing.
The worker functions associated with data, people, and things are listed below. The USTES has used these worker functions as a basis for describing over 30,000 job titles in the DOT.
As with questionnaires and interviews, work log structure should be standardized to assure that gathered data from different employees is comparable. Work logs basically ask workers to keep a running record of what specific things they do on the job. If kept over an entire job cycle, these logs are an excellent way to gather detailed and accurate data on what and when work is accomplished. They are particularly useful for detecting the frequency or repetitiveness of different tasks. Questionnaires and interviews sometimes overlook certain key, but infrequently or randomly per formed, tasks. A disadvantage is that employees can easily distort what they report for reasons of self-interest.
Work logs are unpopular. Workers may find that they are disruptive, time consuming, and a burden. The analyst must do a thorough job to get incumbents to accept the idea of completing a log and to get incumbents to do work on them consistently and accurately. Resistance can be minimized by pointing out the valuable insights logs can give workers into their own usage of time. Logs can really help workers become more efficient. Resistance can also be reduced by instructing the worker in how to fill out the logs. For example, log recordings need not be made after each individual act engaged in by the worker.
Employees can usually wait until mid-morning, noon time, mid-afternoon, and the end of the workday to do their fill-ins for the time periods immediately preceding these points in time. Also, workers should understand that very brief statements are usually all that are necessary to provide a clue as to what went on. Later on the analyst, during an interview perhaps, can fill in the details if necessary. Use of a pre-categorized task log can further reduce employee resistance because such an instrument requires essentially just a check mark to pinpoint the kind of task being completed.
Direct (continuous) Observation
Direct observation of work is a valuable way to gather job data, especially when the worker is in a fixed location and is performing very observable tasks-that is, tasks other than think work, writing reports, and such. Assembly-line workers are a good example of a case where observation would pay off. The analyst must be able to distinguish relevant acts (behavior) from irrelevant ones, and be able to accurately record their observations. The analyst must also take care not to interfere with the behavior of the worker. This is probably the greatest weakness of observation techniques. Of course the analyst must stay out of the way, but there is more to it than this. The presence of the observer usually distorts the performance of the worker unless the worker is fully and properly prepared for the observation scheme. Workers slow down, speed up, or otherwise change their behavior to facilitate their self-interests—whether subconsciously or consciously. Some speed up to impress the analyst. Others slow down because they fear data will be used to set time standards or the like.
Generally, direct observation gives the most accurate and fullest indication of what a worker does. Other methods tend to provide data indirectly, which can be a great source of distortion, amplification, or filtration of the true picture. But direct observation is extremely expensive; it is the most time consuming of all methods if complete work cycles are to be observed.
See the following articles for more information: